化工行业的仓储作业大进大出比较多,SKU种类相对较少,对准确率要求高,但很多企业管理方式粗放,精细化程度不高。对作业效率要求较低。近年来人工成本不断上升,人员流动性增加,一部分化工企业通过上线WMS仓库管理系统来提高仓储物流的管理水平。
化工仓储管理有相应行业特殊性,例如化工物料和零售、机械等物料不同,包括各种颗粒状、粉末状、液体等。有很多固体包可能会按重量出入库,整包会有拆包的情况,液体也可能按容积进行出入库,增加了管理的复杂度。物料一般会启用批次管理,方便进行先进先出和追溯管理。另外有部分化工原料属于危险品,需要区分存放,为避免事故,不能使用RF条码扫描方式进行管理。
物料:
1)包括固体、液体,存放位置可能为固定或不固定。
2)容器一般有袋、液体桶,一般会有多种规格。另外可能会按托盘来管理,管理托盘容器。
3)很多企业按重量采购,需要同时管理重量和包双单位。
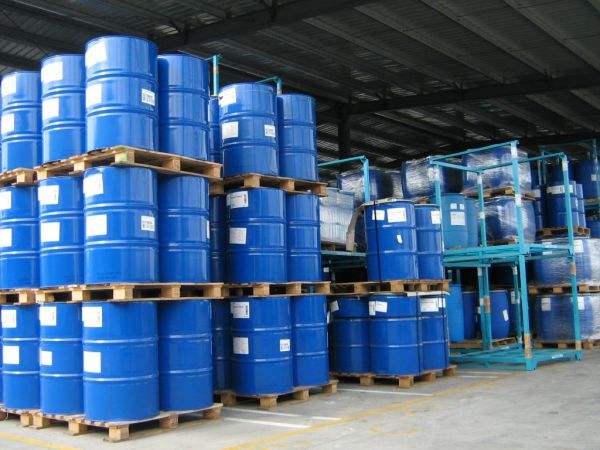
入库:
成品仓,产线贴标码盘后送往仓库,仓库清点物料号、批次、数量信息,根据来货实际数量按整托/零托(散件)入库。自有工厂来货,很多仓库不验货直接收货入库。
原料仓,需要进行质检清点。很多原料需要入检验室进行化验,ERP或MES会把质检结果推到WMS系统,仓库根据质检结果区分物料是否为良品、次品、等级、限用等,并分别处理。
上架:
如果仓库库位容量足够大,SKU变换不频繁,仓库一般会使用固定存放位,好处是管理简单,不易出错。单在出入库数量变化大,空间不足的情况下,这种存放方式就有很大局限性了,需通过系统的辅助来实现灵活的存放。在这种情况下,WMS根据预设上架策略进行最优化建议和智能指引,上架员通过查看PDA或纸质单据上打印的推荐库位进行上架。WMS的策略包括库位/地堆容积,危险品/非危险品分别存放,类别区分,货品防火等级、摆放禁忌、历史存放库位,是否允许混放SKU,是否允许混放批次等多种维度,不同企业根据自己的实际流程选择使用相应策略。
库内:
库内的常规作业包括盘点、库内移库,库内理货、库内上下架、库内冻结库存,库内加工(如贴标)等。
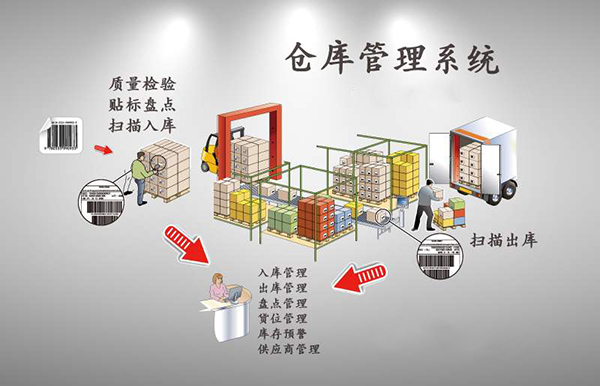
拣货出库:
化工出库量大,一般都是按订单拣货,整托出库。一单货量大的情况可能要几天才能出空,拣货后系统立即扣减库存。拣货有拆托零拣的情况,有的精细化工企业会把整袋拆开进行零数的称重,出库备货区需要配备电子秤。根据批次FIFO先进先出原则拣货下架。
如果是成品仓,一个客户多张订单可按客户合并拣货。一条线路送多个客户,也有按车辆线路拣货的情况。如果是原料仓,用量少的物料可能会根据多条产线的领料单进行波次总量拣货,二次分拣,提高拣货效率。WMS系统会根据系统拣货策略、批次策略、波次拣货策略进行多维度计算,为拣货员推荐最优拣货库位,拣货员根据系统智能指引进行拣货,可极大提高拣货准确率和效率,拣货时无需思考和判断,实现傻瓜式操作。
退货:
在原材料仓存在领料退,车间剩余料打包,标注重量、批次信息后退回存放。有的化工厂因为存储要求,有的物料余料必须返回原料仓存储。
运输交接:管理3PL运输公司装箱/装车,记录运输车辆信息。
综上所述,WMS仓库管理系统需要针对化工仓库的这些特性进行流程设计和配置,满足不同管理要求,提升整体化工仓库管理水平,实现智能化、精益化、可视化的仓储管理。系统智能指引出入库各项作业,新人快速上手。另外条码化作业可有效避免操作错误。通过绩效报表数据分析,可掌握仓库人效和作业瓶颈,方便管理人员进行流程和人员配置的优化。配合使用AGV小车、DPS电子标签设备、自动化立体库等,可实现自动化管理,有效提高仓库效率,降低作业负荷和人工成本。